Design Case Study: J.D. Edwards Seeks Economical Solutions to Global Networks
Contents
Network carefully designed for expansion
Futureproofing multi-mode fiber, cable, and cat 5 backup
Matrix design saves company big dollars
Parts that fit together—what a concept
Designing and installing its corporate network was an important strategic initiative for J.D. Edwards, an enterprise business-software developer. "We needed to design a communications network support infrastructure that would accommodate a company that has doubled in three years and that would become standard for our 46 satellite offices," said John Williams, J.D. Edwards' technologies facility manager.
The company put its vision into practice when installing the network at its new corporate headquarters in Denver. The end result was an innovative, highly functional, and cost-effective cable management system for an estimated 1.25 million feet of cable laid at the new facility.
J.D. Edwards has emerged over the last few years as one of the worldwide leaders in the market for enterprise resource planning (ERP) software. Since 1996, J.D. Edwards has grown from revenues of about $480 million to about $950 million today. During this period of rapid growth, the company has established business relationships with more than 5,500 customers in 100 countries worldwide. J.D. Edwards itself has about 5,600 employees scattered throughout its 46 offices worldwide, with about 1,000 employees at its new headquarters in the Denver Technology Center.
Network carefully designed for expansion
According to Williams, the company's planners spent an enormous amount of time designing the network so that it was easy to expand and reconfigure, and also easy to maintain remotely. He said that easy expansion was achieved by a logical cabling structure that kept cable runs from telecommunications closets to an average of about 70 feet each, or about one-half the length of typical installations.
The network needed to be easy to maintain remotely, which required a decision to standardize upon support systems and cabling used in the infrastructure. In this way, employees at remote facilities would see structures that look identical, making it far easier for headquarters technicians to work with employees at remote offices to troubleshoot problems.
"Let's say one of our remote sites needs to add a new workstation to its communications infrastructure," said John Musial of J.D. Edwards' project implementation group. "Any employee at that site can contact our Denver headquarters and talk with a corporate cabling technician who, in turn, can walk into one of our local IDFs and tell the employee exactly where to patch the cables at a remote facility."
Futureproofing multi-mode fiber, cable, and Cat 5 backup
J.D. Edwards had to think of the big picture in its cabling architecture. Corporate headquarters had more than 200,000 square feet and was only one of several buildings on the company's 53-acre complex, needing more than 1.25 million feet of cable at the new facility alone.
The company's first choice was the one that almost every company faces these days—fiber or copper. The structure itself began with a main distribution frame (MDF) where the key networking systems are located. Two intermediate distribution frames (IDFs) were located on each floor. Finally, the company installed 18 fixed-location power poles per floor that included a cubicle distribution frame (CDF) and a Holocomm Systems (San Diego) vertical-panel control module.
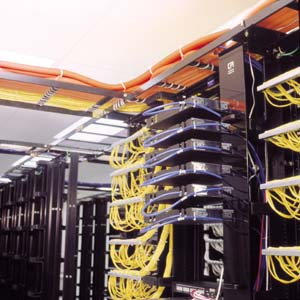
After a lengthy analysis in which the company determined that running fiber would cost more than $35 more per workstation versus copper, Williams said that J.D. Edwards decided to use fiber optic cable for links from the MDF to the IDFs for data traffic, with Category 5 unshielded twisted-pair (UTP) cable as a backup, and Category 5 UTP cable from the IDFs to the CDFs. Voice was handled by Category 3 UTP. He said that he believed that Category 5 cabling could handle the 1 Gb bandwidth requirements that were anticipated at each workstation.
The cable itself was run in 2-ft. increments, making it easier to run the cable from the ceiling down to the power poles and to the CDFs. Patch cords were run from the CDFs to the workstations. This made it easier to handle moves and changes because all connection options take place at the CDFs. It eliminated the need to run cables to the IDFs and then to the MDF for new installs. All a staffer had to do was connect a patch cord to an available slot in the each CDF.
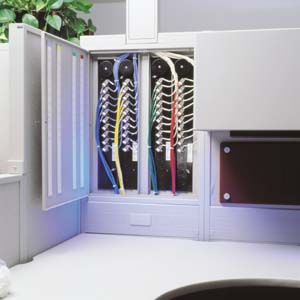
Matrix design saves company big dollars
One of the key goals of the project was to standardize on support structures so that technicians at remote facilities would see identical environments. To meet its needs in this area, J.D. Edwards chose the CatRack cable management system from Chatsworth Products Inc. (CPI ) of Westlake Village, CA. "In all the product comparisons, the CPI CatRack high-density standard racks provided the best base to support our systems solutions," said Musial. "I have been working with the CPI systems approach for the past several years, so it was a natural progression to go with CPI for our installation."
J.D. Edwards also chose The Siemon Co. (Watertown, CT) to supply the cabling systems and Lewan & Associates (Denver) to handle the actual cable installation, working with a local Graybar office and with Siemon. Musial added that the plan included a high-density matrix that would allow the system to support a maximum number of people on each floor with the ability to relocate them easily. He estimated that the matrix design would save the company approximately $500,000 over the next five years.
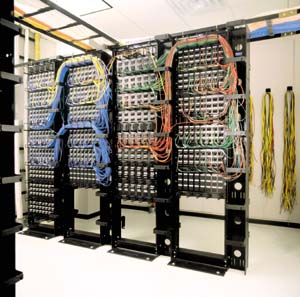
In order to maintain cable integrity over long runs from the IDFs to the CDFs, the J.D. Edwards installation team used a messenger wire support system under fixed cable trays along the ceiling. Wiring similar to that used in electrical fences was tightly ratcheted to the ceiling and the Category 5 cable was secured to the wiring using simple wire ties.
To prevent sensitive equipment from being touched when making cable moves, adds, and changes, the J.D. Edwards team used Category 5 harness cables in which data lines are connected to the equipment via patch panels. When a technician makes an add, move, or change, the connection is made at the panel, not at the equipment termination ports.
Parts that fit together—what a concept
After the system was designed, J.D. Edwards and its contractors set a very tight installation schedule. Marc McGinnis, the operations supervisor for Lewan, reported that the installation was completed in about five weeks, including laying the cable; wiring the MDFs, IDFs, and CDFs; and installing all the rack systems and equipment.
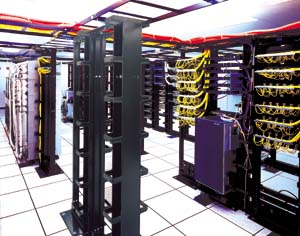
CPI's rack systems were reported to play a significant role in the quick installation process because of the ease with which they were able to be installed and their ergonomic features, such as smooth corners. "It's the little things that make or break you in a major installation project like this," commented Musial. "Installation time is significantly reduced when parts fit together perfectly, when corners are smooth so installers don't cut their hands, and when the cable runway allows a comfortable quarter-inch space so that fingers can fit easily between cable ties and cross sections."
Craig Cottrell, Lewan's project manager for the installation, added, "Time was a critical factor in this project. CPI's products, technical support and attention to every detail made our job move more quickly, and made it much easier."
About the author:
James Dorsett, registered communications system designer (RCDD), is the strategic business planning manager at Chatsworth Products Inc. CPI uses a systems approach to solve the need for companies to organize, store, and secure computer and communications equipment. Their line of LAN/data racks, MegaFrame Cabinet Systems, Structured Termination Systems, and cable management and support systems are offered through an international network of distributors. For more information visit their web site at www.chatsworth.com, via email at info@chatsworth.com or visit <%=company%>.